feed mix for iron ore sintering

VERTICAL INTENSIVE MIXING FOR PROCESSING FINER IRON ORE .
Sep 01, 2014 · DOI: /x25342 Corpus ID: ; VERTICAL INTENSIVE MIXING FOR PROCESSING FINER IRON ORE IN SINTER PLANT inproceedings{Ludivine2014VERTICALIM, title={VERTICAL INTENSIVE MIXING FOR PROCESSING FINER IRON ORE IN SINTER PLANT}, author={P Ludivine and Nouaille .


Sinter plant
Main feed into a sinter plant is base mix, which consists of iron ore fines, coke fines and flux (limestone) fines. In addition to base mix, coke fines, flux fines, sinter fines, iron dust (collected from plant dedusting system ESP) and plant waste are mixed in proportion (by weight) in a rotary drum, often called mixing and nodulizing drum.


what are the ingredients in iron ore
CHAPTER11 FUNDAMENTALS OF IRON ORE SINTERING. GRANULATION OF SINTER MIX INGREDIENTS A sinter feed with good permeability from ignition until burnthrough is required for efficient operation of a sinter plant In this regard it is necessary to consider the widely held and simplistic view that sinter feeds containing iron ores with high ultrafines ...

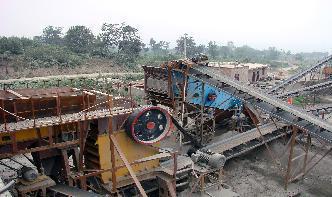
Separation of ultrafine particles using the REFLUX™ Graviton
Jul 24, 2017 · Characterising the mineralogy of iron ore sinters – stateof Improvement of sinter productivity by control of magnetite o Development of an iron ore microparticle binder for increasi Iron sinter process control using Xray diffraction – part : Variation in property parameters of iron ore granulated mix A millipot setup for sintering ...


Iron Ore Sinter
Jul 15, 2014 · Iron Ore Sinter. Iron ore sinter or simply called sinter is usually the major component of a blast furnace iron bearing burden material. Sinter normally consists of various mineral phases produced by sintering of iron ore fines with fluxes, metallurgical wastes and a solid fuel. Coke breeze is normally used as fuel in the sinter mix since it ...


Effect of Mixing Preheated Water on Granulation and Iron ...
Apr 27, 2021 · Thus, to improve granulation behavior of sinter feed mix, various researchers have investigated the factors that affect the granulation process. Iron ore typically constitutes around 54–56% in sinter feed mix and thus its effect on granulation process has been investigated by many researchers.

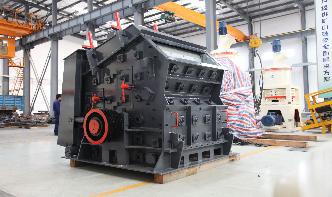
How To Calculate Grain Size From Sintering Temperature ...
Mar 16, 2022 · If you do ten60 minute sintering of iron powder, expect its temperature to be 2050F. As a result of its atomic diffusion process, Sintered particles have either a timelimiting temperature or an enabling temperature. Iron ore can achieve temperatures of 2125F to 2300F during hightemperature sintering.

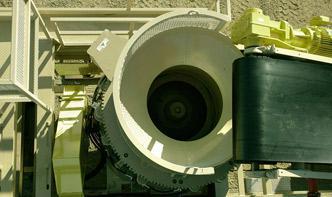
The Sintering Process of Iron Ore Fines
Mar 09, 2013 · The process of sintering begins with the preparation of the raw materials consisting of iron ore fines, fluxes, inplant metallurgical waste materials, fuel and return fines of the sinter plant. These materials are mixed in a rotating pelletizing drum and water is added in order to reach proper agglomeration of the raw materials mix.

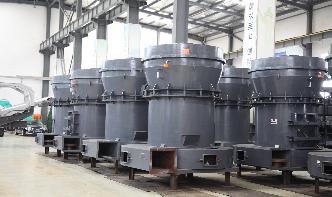
Properties and EndUse Functionality of Iron Ore
Unlike iron ore sinter and pellets which are manufactured from iron ore fines and or concentrate, lump can be directly charged to the furnace without any preprocessing. As a result, lump has an inherently higher value compared with fines due to the avoidance of agglomeration costs. Australia is a significant producer of iron ore lump.

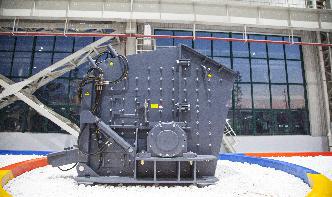
Kinetics of iron ore sinter feed granulation
Aug 01, 1990 · INTRODUCTION Granulation of sinter feed occurs prior to the sintering process. Fine iron ore (8 mm) is mixed with coke, fluxes and screened sinter fines. The mix is granulated in a rotating drum after addition of water. The granules are then sintered as .

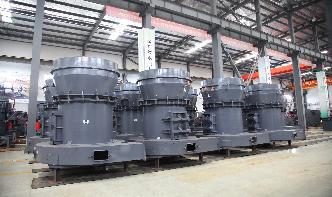
When they were new
Some sintering plants also added iron ore dust and mill scale to the mix (mill scale is a waste product of steel production with high iron content). The resulting product had size characteristics that made it a more efficient blast furnce feed. I've heard the finished product from a sintering plant referred to as "snowballs".


Is Iron Ore A Homogeneous Or Heterogeneous Mixture ...
Nov 17, 2021 · Iron ore homogeneous b. The principle of separating funnel is that immiscible liquids separate out in layers depending on their densities. However this powder is microscopically heterogeneous. Alloy steel is a type of steel which includes iron carbon and some other elements in its chemical composition.


Solutions for mixing and granulating sinter ...
The raw sinter mix consists of iron ore, limestone, coke, sinter return fines and binder. The various materials are fed in the correct ratios from the respective storage hoppers to the mixer where they are mixed and granulated before they are ignited in .

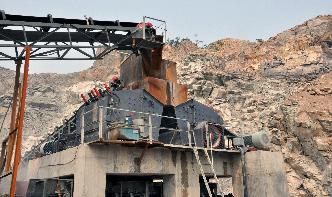
capex beneficiation of iron ore fines
Samples grading 53% iron were beneficiated using simple attrition scrubbing .. A significant reduction in capital expenditure (" Capex ") and .. Highly marketable sinter fines magnetite concentrate of 6669% iron, .. Afferro's portfolio includes the owned Nkout, Ntem and Akonolinga iron ore projects. » More detailed.


(PDF) Iron Ore Sintering: Raw Materials and Granulation
Oct 28, 2016 · the iron ore mix and return fines are placed in the drum; in. ... ties of iron ore sinter feed on granulation effectiveness. ... breeze particle size and its .

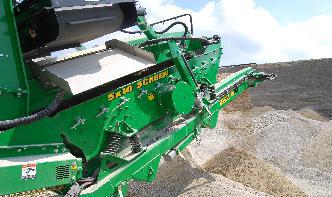
Pollution Effects of Abnormal Operations in Iron and Steel ...
The preferred course is to mix limestone in the sinter feed and use the heat of the sintering process for calcining it. PROCESS FLOW SHEET The sintering process, as described herein, includes receiving, mixing, feeding, and agglomerating the raw materials; the actual sintering operation; and the crushing, screening, cooling, and ...


Modifiion of Wet Granulation Process During Iron Ore ...
Sintering is the most extensively used and economic agglomeration process to prepare iron ore fines for blast furnace use. Granulation is the most critical factor controlling iron ore sintering process, as it improves sinter mix permeability. Currently, sinter plants are receiving significant proportion (up to 40%) of − 150 μm microfines in iron ore fines, which makes sintering difficult.

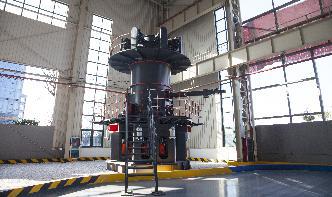
PRO: Brazilian Iron Ore Sinter Feed, Fe % – in Bulk
Oct 02, 2008 · Brazilian Iron Ore Sinter Feed, Fe % – in Bulk COMMODITY Brazilian Iron Ore Sinter Feed, Fe % – in Bulk ORIGIN Brazil – South America AVAILABILITY Metric Tons (+/ 5%) with Extensions DELIVERY /MT until /MT Months PORT OF LOADING Sepetiba Port – Rio de Janeiro – RJ ...


Iron Ore Sintering Process in Steel Manufacturing
Sinter is the primary feed material for making iron in a blast furnace. Sinter is created by mixing iron ore concentrate with several additives such as limestone and silica to control the chemistry and then igniting it at 1200°C in a continuous beltfed furnace.

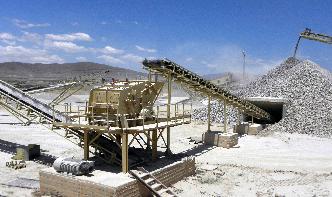
size requirement for iron ore concentrate
Balling: The powdery iron ore concentrate is mixed with a small amount of a clay binder called "bentonite' and rolled into marblesized pellets. Rotary Kiln: Heathardening of pellets at temperatures as high as 2,400 °F. Iron ore Processing diagram [image 135110] Iron ore pellets [image 135112] Iron ore processing flowsheet. Read More

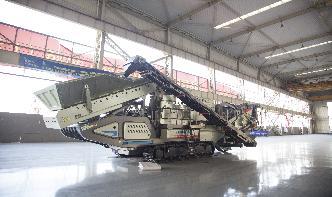
Vale iron ore product mix quality falling after dam burst ...
Apr 02, 2019 · London — Brazilian miner Vale's average iron ore product mix is set to decline in terms of quality following the January 25 dam burst at the company, according to CFO Luciano Siani. The company plans to keep its offer of Brazilian blend fines (BRBF) constant, but its offer of Carajas fines and niche products will decline, he added.
