sand making powder plant iron ore design

How it works: The Blast Furnace
The remaining ironrich powder is rolled into balls and fired in a furnace to produce strong, marblesized pellets that contain 60% to 65% iron. Sinter is produced from fine raw ore, small coke, sandsized limestone and numerous other steel plant waste materials that contain some iron. These fine materials are proportioned to obtain a desired product chemistry then mixed .


Cement Manufacturing Process
Stage of Cement Manufacture. There are six main stages of cement manufacturing process. Stage 1 Raw Material Extraction/Quarry. The raw cement ingredients needed for cement production are limestone (calcium), sand and clay (silicon, aluminum, iron), shale, fly ash, mill scale and bauxite. The ore rocks are quarried and crushed to smaller pieces of about 6 inches.

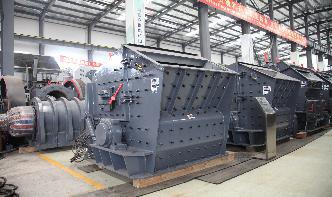
Home • Ore Designs, Inc.
Ore is a design company specializing in the design and manufacturing of landscape architectural elements. We believe that beauty and sustainability are fundamentally linked. Our products and processes are consciously developed to enhance landscapes while preserving environmental integrity. We manufacture our products inhouse and directly ...


co combustion of coal and iron ore powders
Iron ore is the raw material used to make pig iron, which is one of the main raw materials to make steel. 98% of the mined iron ore is used to make steel. Coke is used as a reducing agent in smelting iron ore in a blast furnace The carbon monoxide produced by its combustion reduces iron oxide (hematite) in the production of the iron product.

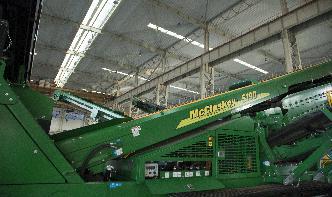
How iron is made
Iron ore is converted into various types of iron through several processes. The most common process is the use of a blast furnace to produce pig iron which is about 9294% iron and 35% carbon with smaller amounts of other elements. Pig iron has only limited uses, and most of this iron goes on to a steel mill where it is converted into various steel alloys by further reducing .

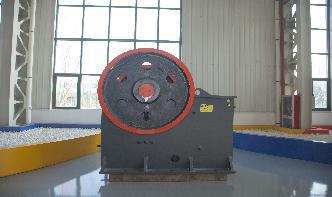
Electrostatic Separation
Mineral Sands. Iron Ore. Coal. Process Solutions. Metallurgical Testing Process Design. Equipment Design Selection. Gravity Separation. Centrifugal Jig Technology . Electrostatic Separation. Magnetic Separation. Shaking Tables, Knudsen Bowl. Process Audits Optimisation. New Products from RD. Plant Design. World's Largest Mineral Sands Plant Design. .

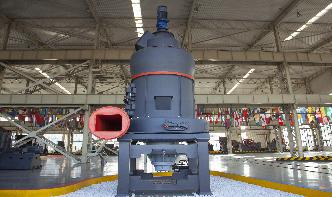
Bitumen Extraction Explained | Oil Sands Magazine
· Each Extraction plant is designed for a certain oil sands throughput assuming an average ore grade. If an excessive amount of oil sands is processed through the Extraction plant (above the design capacity), the residence time within the gravity separation vessel is proportionally reduced and bitumen recovery rates may be compromised. This is especially a .


Talcum Powders Making Plant
Talc Mill for Powder Making Talc Plant. In talc powder production line, we need to make crushed talc grinded into talc powder. Appliion of talc powder is based on the size of talc powder. Talc coarse powder usually is 200 mesh and 325 mesh, and is used for paper making. The super micro talc powder is less than 5 um and mainly used in . which mill is used to .

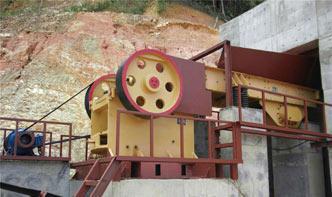
Plant Engineering | Wearresistant ceramic coatings
· Protecting cast iron parts from aggressive chemicals that can eat away at and react with the metal substrate. The coating's epoxy base and ceramic beads are both inert and highly resistant to chemical attack. By making wear predictable, ceramic coatings vastly improve the lifespan of pumps and reduce incidents of unplanned maintenance. These ...

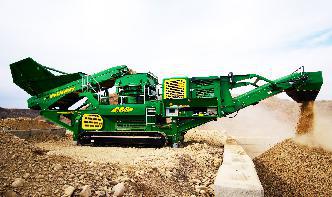
The Steel Manufacturing Process
· Iron ore was first mined in Central Asia and Europe, and humans at this time used iron to make tools and weapons in a practice called ferrous metallurgy. Iron products evolved during this time, beginning with blacksmiths producing wrought iron goods. These tradespeople learned to heat up iron ore, and using a hammerandanvil process, the blacksmiths would .


The Ironmaking Process
The New Zealand Steel plant at Glenbrook is unusual in that the huge blast furnaces that dominate the processes at most steel works around the world are not present. This has eventuated because of the nature of the ore mined locally and used in the process. Early pioneering experiments failed to successfully smelt iron from New Zealand's west coast .

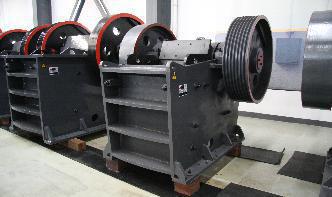
copper ore dressing ore powders making plant
Copper Ore Slag Powder Grinding Mill Aluneth Heavy iron slag powder qatar iron ore ball mill machine to 325 mesh acherishedbirth Jun 16 2018 iron ore ball mill machine to 325 meshStone Powder Making Machineiron ore Gypsum stone Slag grinding mill machine and powder making plant high quality steel mill machine 200 mesh stone powder making . copper gold ore .

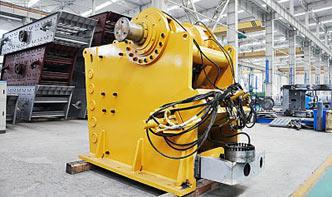
Extracting iron
Iron is extracted from iron ore. in a huge container called a blast furnace. Iron ores such as haematite contain iron(III) oxide, Fe 2 O 3 . The oxygen must be removed from the iron(III) oxide in ...

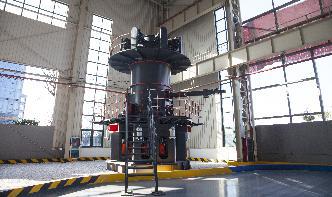
Iron Ore Pellet
This picture is of an early iron ore sintering plant used to agglomerate powder prior to melting to make steel. Today iron ore agglomeration is the largest tonnage appliion for sintering, with plants operating at up 20,000 metric tonnes per day. For example, Figure is a picture of a modern agglomeration facility which incorporates offgas capture to reduce environmental .

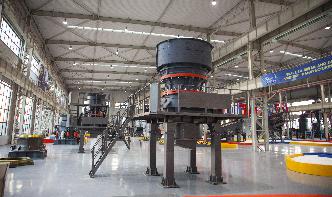
Steelmaking
Steelmaking has played a crucial role in the development of ancient, medieval, and modern technological societies. Early processes of steel making were made during the classical era in Ancient Iran, Ancient China, India, and Rome.. Cast iron is a hard, brittle material that is difficult to work, whereas steel is malleable, relatively easily formed and a versatile material.
