steel melting shop process flow sheet
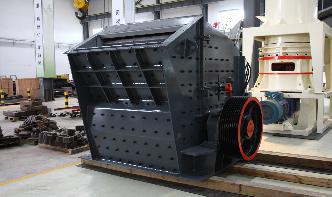
Determining the flow stress curve with yield and ultimate ...
May 11, 2011 · The flow stress curve, which reflects the sheet material's elastic and plastic properties, typically is obtained from a tensile test or bulge test. 1 In a tensile test, a standardsize specimen is cut out from the sheet metal and pulled slowly until it breaks. An extensometer is attached to the specimen to measure the elongation over an ...

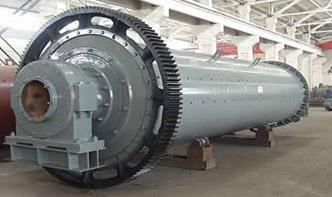
Die Casting Process, Defects, Design
7. Design Rules. 8. Cost Drivers. Die casting is a manufacturing process that can produce geometrically complex metal parts through the use of reusable molds, called dies. The die casting process involves the use of a furnace, metal, die casting machine, and die. The metal, typically a nonferrous alloy such as aluminum or zinc, is melted in ...


Steel Forging Tempering Chart
The forging process involved molding the knife at a critically high heat level (typically 900 2,000 degrees Fahrenheit) to improve its hardness. Once you are done forging the knife you can move on to the tempering process in which you increase the knife's flexibility and sharpness at a lower temperature, typically between 390 800 degrees ...

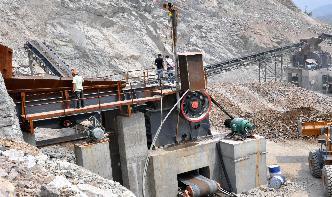
Production Manufacturing Process Flow Charts ...
The production process, or manufacturing process, consists of a few key components or subprocesses from production planning through quality assurance and inspection of final products. Manufacturing process flow charts, or workflows, can be applied to the manufacturing process to reduce lead times, increase machine utilization and optimize first pass yields.

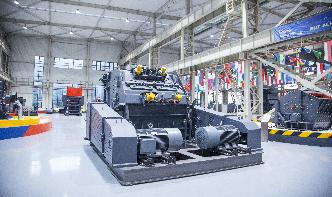
steel
steel steel Basic oxygen steelmaking: More than half the world's steel is produced in the basic oxygen process (BOP), which uses pure oxygen to convert a charge of liquid blastfurnace iron and scrap into steel. The basic oxygen furnace (BOF) is a refractorylined, tiltable converter into which a vertically movable, watercooled lance is inserted to blow oxygen through nozzles .


The Float Process
The melting process is key to glass quality; and compositions can be modified to change the properties of the finished product. Stage 2: Float bath Glass from the melter flows gently over a refractory spout on to the mirrorlike surface of molten tin, starting at 1,100°C and leaving the float bath as a solid ribbon at 600°C.


Manufacturing Systems Cheat
Manufacturing Systems Cheat Physical Process used to shape material: Deformation, Material Removal, Melting/Solidifiion, Joining, ... Abrasive Flow Machining ... increased accuracy on complex features and expanded shop capability Machine Types: 2 Axis – Lathe, 3 Axis – Mill, 4 or 5 Axis ...


6 Common Sheet Metal Forming Process
Jul 11, 2019 · Sheet metal often contains sharp edges with "burrs" after it's initially produced. Curling is a forming process that involves deburring sheet metal to produce smooth edges. #2) Bending. Another common sheet metal forming process is bending. Companies typically perform bending on sheet metal using either a brake press or similar machine ...

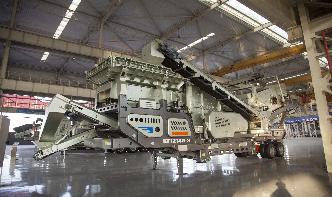
Technical Manual: Hood System Capture of Process Fugitive ...
SELECTED VENTILATION SYSTEMS FOR PROCESS FUGITIVES IN VARIOUS INDUSTRIES Industry Iron and steel Sharon Steel Corporation Crucible, Sidbec Melt Shopb Knoxvllle Iron Company*" oo HI Carpenter Steel (Reading, PA)d «5 * StelcoMcMaster Melt Shop8 Iscott (Trinidad)6 * Chaparral Steel (Texas) Process fugitive source Electric arc furnace (2 ...

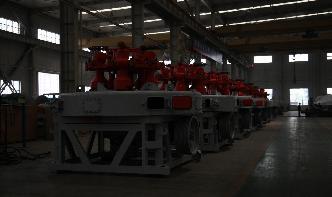
Using Cast Iron for Steel Melting in an Electric Arc ...
Feb 11, 2020 · The Conarc process is more versatile than others, due to the multivariance of the possible operating modes: purely electric steel melting with a consumption of solid cast iron up to 20–30% or liquid—up to 80%; pure converter with a consumption of liquid cast iron of 70–80%; and mixed with any ratio of scrap, solid or liquid iron products ...


Modern Sheet Metal Forming In The Automotive Industry ...
Jan 01, 2015 · The metal flow is restricted by the die contours, this allow more difficult shapes to be created. ... The material then will melt or burn currently they are used to cut, form holes. The advantages of using laser cutting are accuracy and great consistency in the product being made. ... In this process the sheet metal is stretched and ...

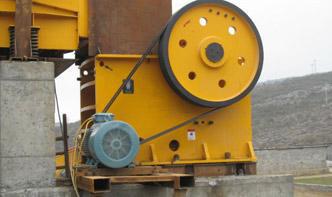
DIY Metal Melting Furnace : 3 Steps (with Pictures ...
Step 3: Final Pieces. Now to make the hole for the air flow take the 1" hole saw and start drilling into the side of the bucket a couple inches from the bottom once through the metal tilt down and drill down at about a 25 to 30 degree angle so that if a .


Overview of metal casting for beginners
Sep 16, 2016 · For this process, you will need to burn the molds out in a kiln to melt out, burn off, and finally vaporize the wax, as well as calcining the molds. You need to run it for a few days and slowly ramp up the temperature, eventually keeping the molds at 1200 for a day and filling them with molten metal when they cool to around 800.


HeatKing™ Products for Steel Melting in Coreless Induction ...
Feb 02, 2020 · Improvement in melt shop and maintenance interval planning; Working lining exhibiting low reaction with the metal or slag; Higher metal purity thanks to higher chemical resistance and less inclusions in finished metal; Compatible with metallurgical treatment of the metal in the coreless induction furnace, dephosphorization process


Metal Casting Process
A mold is formed into the geometric shape of a desired part. Molten metal is then poured into the mold, the mold holds this material in shape as it solidifies. A metal casting is created. Although this seems rather simple, the manufacturing process of metal casting is both a science and an art. Let's begin our study of metal casting with the mold.


The Powder Coating Process
Sep 29, 2011 · In pursuit of a sprayable, lowVOC coating, Dr. Pieter g. de Lange of The Netherlands developed the process of hot melt compounding in a zblade mixer. This made powder coating materials much more consistent and provided the opportunity for thinnerfilm thermoset products that could better compete with liquid coatings.


How Is Stainless Steel Made? | Metal Supermarkets
May 25, 2016 · Stainless steel is known for excellent corrosion resistance. It is an integral part of modern life and is used in a range of appliions, including heavy industry, architecture, automotive manufacture, surgery and dentistry.. Until the 1950s and 1960s, which saw the development of AOD (argon oxygen decarburization) and VOD (vacuum oxygen .


A Quick Guide to Annealing: What is Annealed Metal?
Jun 30, 2020 · Sheet metals, such as cold rolled steel sheet and galvanized steel sheet, are annealed because the process of cold rolling creates too much hardness for further processing. Annealing restores their ductility and formability, which allows for further bending, punching, forming/stretching or cutting without cracking or losing dimensional stability.

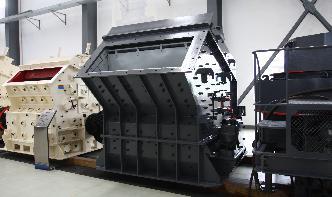
Steel Melt Shop Equipments
Remso is a world leader in the manufacturing of Ladle Transfer Car. A ladle transfer car is a molten metal handling tool which is used in foundries Steel mills. The Ladle car carries a metal ladle carrying hot metal from one loion to another for processing of molten liquid metal. It can also be called a molten steel transporter.


TIG Welding
Jan 18, 2022 · The gas begins to flow and starts protecting the weld area from the air. The torch is held over the weld joint just far enough for the torch not to touch the metal. Then the welder presses a foot pedal and the TIG torches tungsten electrode starts an arc. Once the arc is started the two pieces of metal begin to melt by creating a puddle of metal.
